Nickel Alloy 825
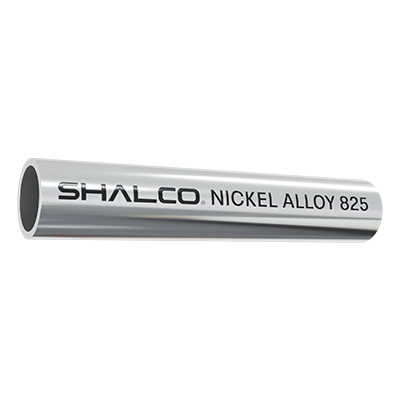
Nickel Alloy 825
Inconel 825 is a highly versatile nickel-iron-chromium alloy, further enhanced by the addition of molybdenum, copper, and titanium. This unique combination of elements gives Nickel Alloy 825 exceptional resistance to a wide range of corrosive environments, including oxidizing and reducing agents.
Its ability to withstand various conditions makes it a popular choice for industries such as chemical processing, marine engineering, and pollution control equipment. The alloy’s microstructure, based on a face-centered cubic cell with a matrix phase, contributes to its superior mechanical strength and durability.
The high nickel content in Nickel Alloy 825 ensures resistance to chloride-induced stress corrosion cracking, while molybdenum enhances its ability to resist pitting and crevice corrosion. Chromium adds protection against oxidizing agents, and copper strengthens its resistance to sulfuric and phosphoric acids.
Alloy 825 is particularly suitable for applications involving sulfuric acid, phosphoric acid, and nitric acid environments. Its resistance to intergranular corrosion, even after welding, is an added advantage, making it a preferred material for demanding projects. Due to its excellent corrosion resistance and robust mechanical properties, Inconel 825 is widely used in heat exchangers, piping systems, and nuclear fuel reprocessing plants. Nickel Alloy 825 continues to play a critical role in providing reliable performance in the most challenging environments.
Specifications
The carefully engineered chemical composition of Nickel Alloy 825 delivers exceptional resistance to various corrosive conditions, making it a reliable choice for critical applications. This alloy is designed with nickel, chromium, and iron as its primary components, further fortified by molybdenum, copper, and titanium. These elements work synergistically to combat aggressive environments effectively, including those prone to pitting, crevice corrosion, and stress corrosion cracking.
In Inconel 825, the addition of titanium forms a stable titanium oxide layer, which acts as a protective barrier against localized attacks. This property ensures excellent performance in environments containing chlorides and reducing acids. Industries handling sulfuric, phosphoric, and nitric acids often rely on Nickel Alloy 825 for its outstanding durability.
Alloy 825 exhibits superior resistance not only to oxidation but also to reducing environments, providing versatility across applications. It performs well in chemical processing equipment, heat exchangers, and marine environments, offering long-term reliability. The high nickel content further prevents stress corrosion cracking, even under harsh conditions.
With its remarkable ability to withstand extreme corrosive forces and its robust mechanical properties, Inconel 825 is a preferred material in industries such as oil and gas, pollution control, and marine engineering. Nickel Alloy 825 remains a cornerstone for applications requiring unmatched resistance and durability.
[#corrosion-resistance]Nickel Alloy 825 Corrosion Resistance[#corrosion-resistance]
Inconel 825 (UNS N08825 / W.Nr. 2.4858) is a highly versatile nickel-based alloy known for its exceptional resistance to both reducing and oxidizing acids. With a unique chemical composition including nickel, chromium, molybdenum, copper, and titanium, this alloy is specifically designed to combat a wide range of corrosive environments effectively. Its ability to resist stress-corrosion cracking, pitting, and crevice corrosion makes it an invaluable material for demanding industrial applications.
The high nickel content in Nickel Alloy 825 provides resistance to chloride-ion stress corrosion cracking, while the inclusion of molybdenum and copper enhances its strength against reducing acids like sulfuric and phosphoric acids. Additionally, titanium stabilizes the alloy, forming a protective oxide layer that safeguards against localized attacks.
Alloy 825 is particularly effective in environments involving seawater and other aqueous solutions, where it offers improved corrosion resistance compared to similar alloys, such as alloy 800. Its excellent performance in water-related applications makes it a reliable choice for industries such as marine engineering and pollution control.
Inconel 825 is widely used in chemical processing, heat exchangers, and piping systems where durability and resistance are paramount. The robust chemical composition of Nickel Alloy 825 ensures long-lasting performance even under the most extreme conditions, reinforcing its status as a top-tier material for critical applications.
Physical Properties of SS 825
[#fabrication-and-heat-treatment]Nickel Alloy 825 Heat treatment[#fabrication-and-heat-treatment]
When we consider Inconel 825 Vs. Incoloy 825, Incoloy 825 alloy products are heat-treated during the manufacturing process to develop a proper composition of stabilization, corrosion resistance, mechanical properties, and formation. To maintain these properties during fabrication, subsequent annealing must be done in between 1700 to 1800°F (930 to 980°C) followed by rapid air cooling or water quenching.
[#hot-forming]Nickel Alloy 825 Hot forming[#hot-forming]
The hot-working temperature range for Incoloy alloy 825 is 1600°F to 2150°F (870°C to 1180°C). For ideal corrosion resistance, last hot working ought to be done at temperatures somewhere in the range of 1600°F and 1800°F (870°C and 980°C). Cooling after hot working ought to be air cool or quicker.
Content of titanium in nickel alloy 825 remunerated against sharpening in the as-welded condition. It builds its resistivity to intergranular corrosion after temperatures are in a reach that would make stable solidified stainless steels.
The alloy 825 has less working hardness due to the copper content. It can hence be used at cryogenic temperatures to high temperatures without any loss of mechanical properties. The composite 825 is popularly used around 540°C, with no adjustment in its microstructure and flexibility.
[#machinability]Nickel Alloy 825 Machinability[#machinability]
Inconel 825 is moderately simple to machine. All the standard techniques can be promptly utilized. It has ideal machining attributes in the tempered condition. The nickel alloy 825 is determined as ‘C’ alloys and tooling particulars are moderately utilized. Positive feeds, inflexible tooling, proper velocities, satisfactory oiling, or lubrication will give ideal outcomes.
[#weldability]Nickel Alloy 825 Weldability[#weldability]
Inconel Alloy 825 is readily weldable by the normal processes such as (GMAW (MIG), GTAW (TIG), SMAW (manual), SAW) during welding the joint must be clean to avoid contamination of the weld pool.
Nickel alloy 825 can be suitably welded by the protected metal circular segment.
The method of using alloy welding anode 135, the gas protects bend procedures utilizing combination filler metal 65, and the obstruction welding forms.
[#applications]Nickel Alloy 825 Applications[#applications]
Specific Applications of Inconel 825
- Condensers in heat exchangers
- Oil and gas well equipment on the seashore
- Hydraulic systems
- Chemical injection lines
- Chemical process equipment and vessels
- Downhole control lines
- Control and instrumentation
- Acid Production
- Nuclear fuel processing
General applications of Incoloy 825
- Sulphuric acid piping and vessels
- Phosphoric acid evaporators
- Pickling tank heaters, pickling tanks, and equipment
- Chemical process equipment
- Propeller shafts
- Tank trucks
- Calorifiers
- Electrostatic precipitator electrodes
- Hot vessels for food, water, and seawater,
- Ammonium sulfate vessels
- Expansion bellows
- Marine exhaust systems
- Power station ash hoppers
NOTE: Inconel 825 is a registered trademark of Special Metals Corporation.
Chemical processes
Furnaces Vacuum
Not able to find what you are looking for?
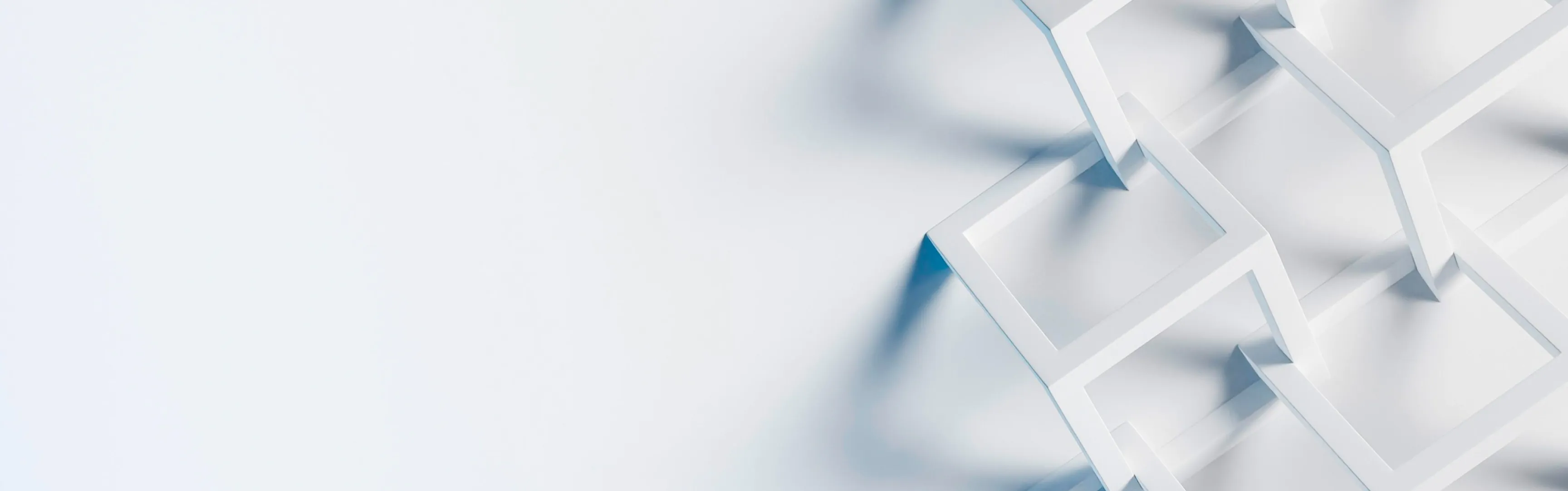