Nickel Alloy 601
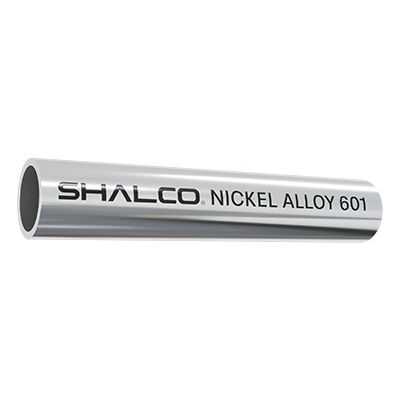
Nickel Alloy 601
Inconel 601 is a nickel-chromium-iron alloy with a face-centered cubic structure, designed for superior performance in environments requiring resistance to extreme heat and corrosion. The alloy exhibits exceptional metallurgical stability, with its microstructure comprising phases such as chromium carbides and titanium nitrides, which contribute to its durability and reliability in demanding applications.
A hallmark of Inconel 601 is its outstanding resistance to high-temperature oxidation, making it a preferred material for applications involving prolonged exposure to heat. The high chromium content in Inconel 601 enhances its ability to form a tightly adherent oxide layer, protecting the material from oxidative damage even in extreme thermal conditions.
This makes it particularly useful for applications such as heat exchangers, furnace components, and gas turbine parts. Inconel alloy 601 also demonstrates excellent resistance to aqueous corrosion, making it versatile for industries requiring both thermal and corrosion-resistant properties.
Nickel Alloy 601 stands out for its superior mechanical strength and ease of fabrication. The alloy can be readily formed, machined, and welded, providing flexibility in manufacturing complex components. This makes Inconel 601 an ideal choice for industries like aerospace, chemical processing, and power generation, where durability and performance under challenging conditions are critical.
Inconel alloy 601’s remarkable combination of high-temperature resistance, corrosion resistance, and mechanical strength ensures its continued relevance in advanced industrial applications. Its ability to maintain structural integrity and performance even in the harshest environments highlights the value of this advanced material.
Physical properties
[#oxidation-resistance]Inconel 601 Oxidation Resistance[#oxidation-resistance]
Inconel 601 Oxidation Resistance
Inconel 601 is renowned for its exceptional oxidation resistance, even at high temperatures reaching up to 1250°C. This unique property makes it a reliable choice for industries that demand materials capable of withstanding extreme thermal conditions. The alloy develops a protective oxide coating that remains stable and resists scaling, even under the challenging conditions of cyclic exposure to varying temperatures. This oxide layer ensures the material’s longevity and performance, even in the most demanding environments.
The superior oxidation resistance of Inconel alloy 601 is attributed to its carefully balanced composition of nickel, chromium, and aluminum. These elements work synergistically during high-temperature exposure to form a dense, adherent oxide film on the alloy's surface. This protective film effectively shields the underlying material from further degradation, ensuring its structural integrity over extended periods.
Nickel Alloy 601 is particularly valued in applications requiring robust performance under thermal cycling, such as furnace parts, heat exchangers, and combustion chambers. Its ability to resist oxidation under these harsh conditions sets it apart from many other alloys.
Moreover, Inconel 601 exhibits excellent resistance to carburization and sulfur-containing atmospheres, further broadening its suitability for high-temperature applications. Its unparalleled oxidation resistance, combined with mechanical strength and ease of fabrication, makes Inconel alloy 601 a preferred choice for industries such as aerospace, chemical processing, and power generation.
The combination of advanced material properties ensures that Inconel 601 continues to play a critical role in environments where high-temperature resistance and durability are paramount.
[#fabrication-and-heat-treatment]Inconel 601 Heat Treatment[#fabrication-and-heat-treatment]
Alloy inconel 601 promptly shapes a refractory surface oxide during working with heat and can’t be bright-annealed in the standard mechanical furnace. Inconel 601 composition/solution strengthened at 1100°C – 1180°C and cooled rapidly in order to maintain a strategic distance from sensitization to intergranular corrosion. Annealing time ought to be short to dodge extreme grain development.
[#corrosion-resistance]Inconel 601 Corrosion Resistance[#corrosion-resistance]
Inconel 601 is widely recognized for its exceptional resistance to corrosion in a variety of harsh environments. The alloy’s high nickel and chromium content, coupled with aluminum, provides superior protection against chemical attack and high-temperature corrosion. These properties make Inconel alloy 601 ideal for applications exposed to oxidizing and carburizing environments at elevated temperatures, such as furnace components, heat exchangers, and chemical reactors.
The unique composition of Inconel alloy 601 enables it to resist oxidation effectively at temperatures up to 2200°F (1200°C). Its aluminum content enhances its ability to form a tightly adherent oxide film, preventing spalling even under cyclic thermal conditions. This characteristic ensures the alloy’s longevity and reliability in extreme industrial settings.
Specialized pickling methods are required to create bright, smooth surfaces on components made of Inconel 601, given its robust resistance to chemical attacks. This highlights its versatility and suitability for demanding manufacturing processes.
[#corrosion-resistance]Inconel 601 Corrosion Resistance[#corrosion-resistance]
For hot-forming operations, the temperature range for Inconel 601 is 1600°F-2250°F (870°C-1230°C). Heavy deformation should occur at 1900°F-2250°F (1040°C-1230°C), while light working below 1200°F (650°C) is permissible for improving tensile properties. However, the alloy should not be worked between 1200°F and 1600°F (650°C-870°C) due to its reduced ductility in this range.
Nickel Alloy 601 continues to be a preferred choice for industries requiring materials with superior corrosion resistance and mechanical strength at high temperatures. Its ability to maintain performance under challenging conditions makes Inconel 601 indispensable in aerospace, power generation, and chemical processing applications. The combination of thermal stability, corrosion resistance, and versatility ensures Inconel alloy 601 remains a benchmark in high-performance alloys.
Specifications
The pace of cooling following hot-working isn’t basic concerning warm breaking. To maintain a strategic distance from sharpening, be that as it may, the alloy should be cooled quickly through the 1000-1400°F (540-760°C) temperature range.
The AISI 601 stainless steel is cold-formed by customary methods. The alloy’s work-solidifying rate is to some degree higher than the rate for inconel alloy 600 and INCOLOY alloy 800.
[#applications]Inconel 601 Applications[#applications]
Alloy AISI 601 has great creep resistance and strength, and the alloy is broadly utilized for equipment that should withstand stretched out to high temperatures. The alloy’s convenience for such applications is enhanced by its resistance from oxidation and different types of high-temperature corrosion.
- Chemical Processing
- Aerospace
- Heat treating industry
- Power generation
- Heat treating muffles and retorts
- Radiant tubes
- Catalyst support grids in nitric acid production
- Steam superheater tube supports.
NOTE: Inconel 601 is a registered trademark of Special Metals Corporation.
Chemical processes
Furnaces Vacuum
Not able to find what you are looking for?
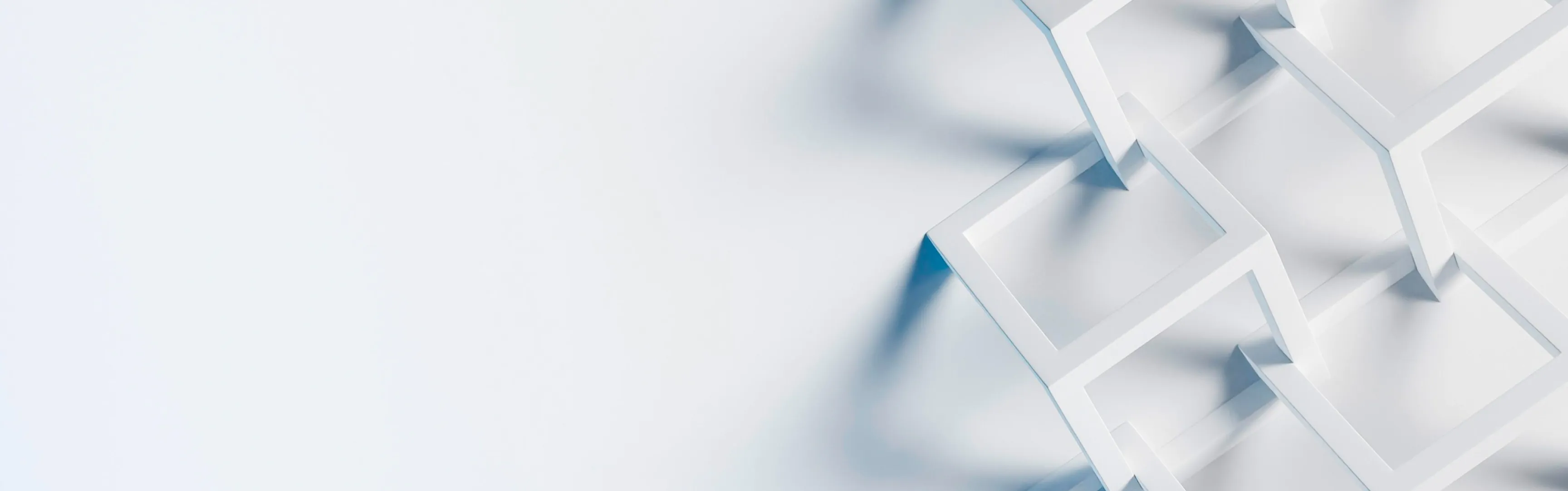