Nickel Alloy 600
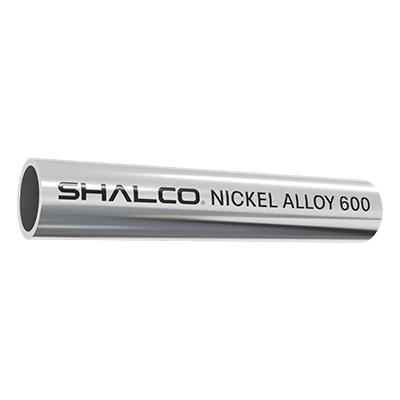
Nickel Alloy 600
Inconel 600, also known as Nickel Alloy 600, is a superalloy with extraordinary properties that make it highly suitable for demanding applications. This nickel-chromium alloy is renowned for its excellent mechanical strength, resistance to oxidation, and superior surface stability.
It is designed to withstand both cryogenic and elevated temperatures, making it ideal for a wide range of industries, including aerospace, chemical processing, and power generation. The material’s ability to perform in extreme environments is largely due to the strengthened solution, which incorporates precipitation strengthening mechanisms.
These secondary phase precipitates, such as gamma prime and carbides, contribute to Inconel 600's outstanding thermal creep resistance. Inconel 600 is particularly valuable for its high resistance to oxidation and corrosion, even in aggressive environments. The alloy’s high chromium content helps protect against oxidation, while the nickel content ensures its stability at elevated temperatures.
This makes Nickel Alloy 600 an excellent choice for use in applications that involve exposure to high heat and corrosive substances, such as heat exchangers, furnace components, and gas turbines. Inconel 600’s face-centered cubic crystal structure, characteristic of many austenitic-nickel-chromium alloys, contributes to its exceptional toughness and ductility.
Its ability to perform reliably in both cryogenic and high-temperature conditions, ranging up to 2000°F (1093°C), further underscores its versatility. This makes Nickel Alloy 600 a crucial material in industries that demand both high temperature and corrosion resistance, ensuring the long-term performance of critical components.
Inconel 600 material is highly resistant to corrosion in many organic acids, such as acetic acid, formic acid, stearic acid, and others. However, it exhibits only medium resistance in inorganic acids. Despite this, Inconel 600 is particularly valuable in the nuclear industry, where it is used in the high-purity water systems of nuclear reactors. Its resistance to corrosion is critical in the first and second recycling stages of high-purity water, helping to prevent the risk of corrosion cracking in such environments. Inconel 600’s excellent performance in these demanding applications can be attributed to its strong chemical composition, which is optimized for corrosion resistance.
However, Inconel 600 material can be susceptible to stress corrosion cracking in environments where high temperatures and caustic alkalies are present. To mitigate this risk, Inconel 600 must undergo complete stress-relieving at temperatures of 1650°F (1 hour) or 1450°F (4 hours) (900°C/1 hr or 790°C/4 hr) before processing. Operating stresses should also be minimized to prevent failure. Furthermore, when Inconel 600 comes into contact with mercury at higher temperatures, it can experience stress-corrosion cracking. In such cases, appropriate service conditions should be applied to avoid damage.
Inconel 600 is widely used in furnace and heat-treating applications, including for parts like boxes, muffles, roller hearths, and retorts that require resistance to oxidation and high-temperature furnace atmospheres. Additionally, its ability to withstand nitrogen at high temperatures makes Inconel 600 the standard material for nitriding containers, highlighting its strength in high-temperature applications.
The Inconel 600 chemical composition includes a high percentage of nickel and chromium, which contributes to its excellent corrosion resistance. This makes it an ideal material for critical applications in environments subject to extreme conditions.
Physical properties
Not able to find what you are looking for?
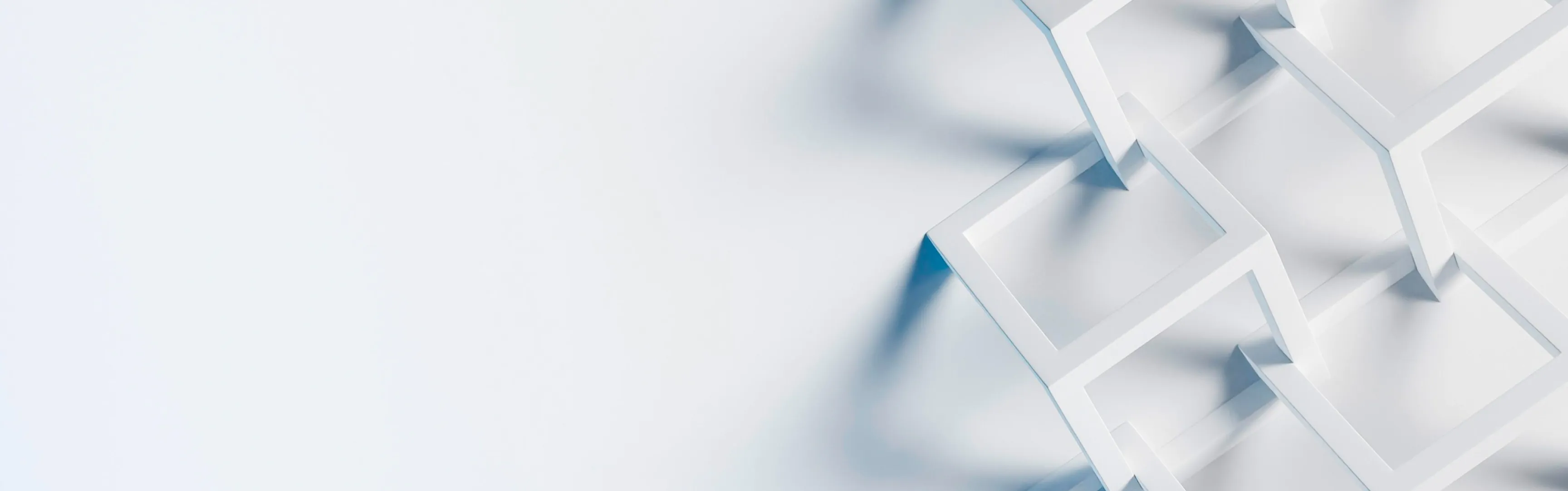